Over 4200 Luxury Cars Destroyed: The Most Terrifying Cargo Ship Disaster Ever Costs Billions
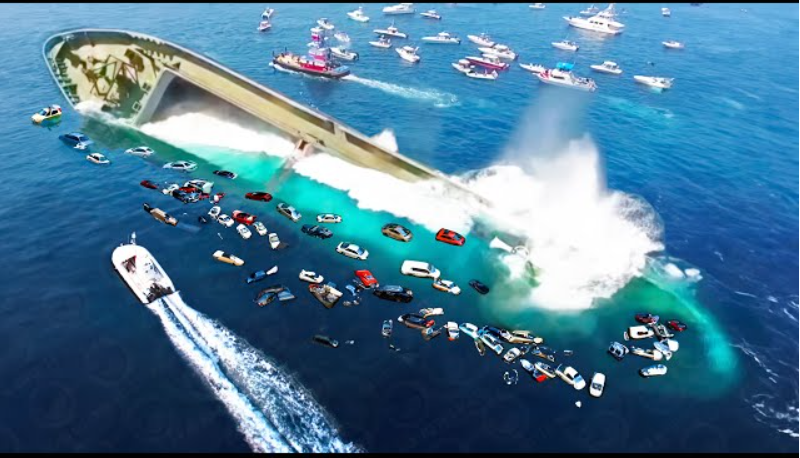
In September 2019, the Golden Ray departed from the port of Brunswick, Georgia, carrying approximately 4,200 vehicles and experienced an electrical disaster. The floating parking garage with a capacity of up to 7,742 vehicles capsized and stranded near the coast of Saint Simon’s Island.
The Coast Guard received an emergency call, helicopters lifted the ship’s crew struggling for survival while support ships unloaded cargo that had not yet fallen into the sea. Lithium-ion batteries and electric cars were at risk of exploding, and most vehicles were stored inside the ship. If a fire broke out, the ship would be under immense pressure. Abandoning the ship is not an adequate option. The risk of oil and fuel leaks now means it is standard practice to try to save the ship and repair the environmental damage.
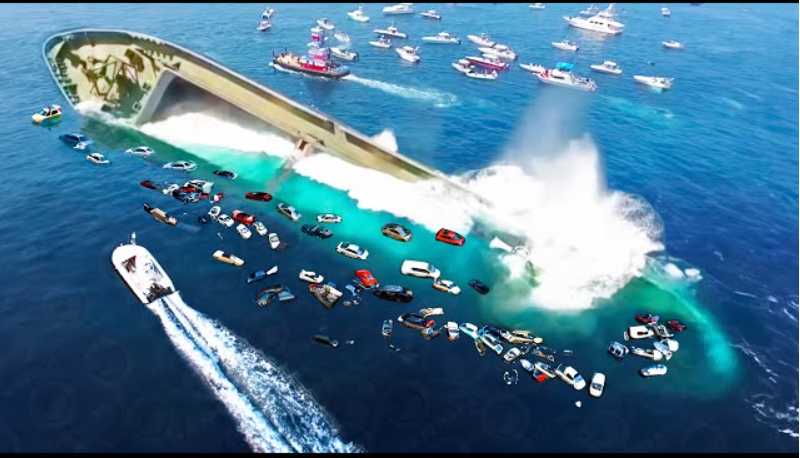
Costa Concordia stranded near Genoa, Italy, in 2012 became the most expensive ship rescue in history, costing over one billion dollars and taking nearly three years, involving 350 rescue workers. There is no standard approach in ship salvage; each operation will vary depending on location, water depth, weather, equipment, and the environmental sensitivity of the surrounding area.
The location of a ship greatly influences how quickly rescue operations can be carried out. The container ship Rena, which ran aground off the coast of New Zealand, had to wait several weeks for equipment to arrive from Singapore. During that time, the ship’s hull was damaged. At this stage, it is still too early to determine the extent of the damage suffered by the Rena’s hull.
In the calm or morning conditions, the rescue team placed a series of equipment such as skirt-shaped cones around the ship to catch fuel and hazardous waste. Meanwhile, a specialized team began pumping more than 20 ship tanks containing over 300,000 gallons of fuel as well as potential contaminants such as lubricants, gases, water, and oily sludge. They drilled through the double steel layers exposed on the outside of the ship to access the fuel tanks below, inserting pipes to pump waste onto waiting vessels .
Divers were sent to enter the interior of the ship and drain the still submerged tanks. This is a sensitive task; removing fuel can make an already unstable ship even more unstable, so this process can take days, possibly months .
After being stuck on the coral reef for several days due to currents, stress fractures appeared along the ship’s hull. These could split the ship into two parts. This dashed hopes of returning the ship to service. The cost of capital recovery was now greater than the value of the ship itself. The mission shifted from a rescue operation to debris removal, and the real work began.
A team consisting of hundreds of engineers, crane operators, firefighters, workers, divers, and architects had to work quickly. They cut away the accommodation blocks to clear the deck and simplify the process. One option for splitting the ship was to use explosives, as was done with the giant container ship MSC Napoli, which ran aground off the southern coast of England in 2007 and was blown into two parts. However, this would be disastrous for the fragile coral ecosystem beneath the shipwreck. Instead, the rescue team decided to split the ship manually using cutting tools and large cranes .
They had to work cautiously and continuously monitor the ship’s stability as they cut and removed parts of the ship from the site. They also had to be mindful of the environmental impact, ensuring that waste or hazardous substances did not contaminate the surrounding waters. This process could take a long time and required tight coordination between all team members.
Once the ship was successfully split, large sections of the ship would be transported out of the area using specialized carrier ships and processed for proper disposal. Alternatively, the removal team chose thick diamond-coated cables that could cut through several inches of steel. The saw was mounted on a custom-made frame that was lifted by a crane and transported to the shipwreck site .
Over two days, both legs of the frame were secured to the seabed on either side of the shipwreck. Inside the frame, the wire moved at high speed through a pulley system and was lowered into the ship’s metal hull, splitting it with a deafening noise. This process could take up to 12 hours to cut through one cross-section, but the saw’s surgical precision ensured that the corals beneath were not damaged. The tool could also cut through parked cars on the lower deck of the ship, minimizing debris falling into the sea as well as cut around fuel tanks .
Fuel was not the only environmental threat; the ship contained an extraordinary load of hazardous materials such as anti-fouling chemicals and lead embedded in the paint, asbestos in the walls, and mercury and polychlorinated biphenols (PCBs) associated with older ship electrical systems. These pollutants would gradually seep out of the shipwreck. A sunken German warship still releases chemicals into the North Sea after more than 80 years .
Now, the Golden Ray is surrounded by ships and equipment ready to intervene as parts of the shipwreck are cut. With the front of the ship stranded on the coral reef but the rear threatening to fall to the seabed when cut, the team has a dual plan. First is the floating shear leg, a giant crane on a floating platform capable of lifting loads up to 7,000 tons. It is a mechanical island with accommodation blocks for dozens of workers who will be at sea for weeks dismantling the ship. Foreign will cut the ship into eight sections, starting from the front. Each piece is punctured with holes through which cables are inserted, then lifted by the crane piece by piece. The ship is carefully loaded onto waiting barges and transported away.
The rear of the ship requires a different approach. Before the rear segment is cut, a support ship attaches a large air-filled metal box called a caisson to its open starboard side. This caisson is partially filled with water, adding weight so that the rear of the ship rotates upright when cut. As the rear of the ship stands upright, a caisson is also attached to its port side. On both sides, the caissons are filled and emptied of water to achieve the perfect buoyancy level to keep the rear of the ship afloat once freed and released into the water. The rear of the ship is then towed to the harbor.
Back on land, parts of the Golden Ray await dismantling. The ship is reported to the European Union, which means it must be dismantled in one of the 46 regulated ports spread across Europe, Turkey, and the United States. This means the ship will be handled in accordance with stricter requirements compared to ships dismantled on the beaches of South Asia, where 70 percent of the world’s ships end their maritime lives. Looser regulations in these locations result in dozens of worker deaths each year and countless environmental impacts as pollutants seep onto the shore and into the sea.
However, at the dry dock in Italy where most of the capsized ship ends up, waste
is supposed to be isolated for several months. The ship is torn back down to its bare bones. Asbestos sheets, cables, equipment, and furniture are removed until only the steel shell remains. This is where most of the ship’s value lies. An efficient smelting operation can recycle almost all of the ship’s steel. Around 90 percent of the materials in the Costa Concordia were recycled.